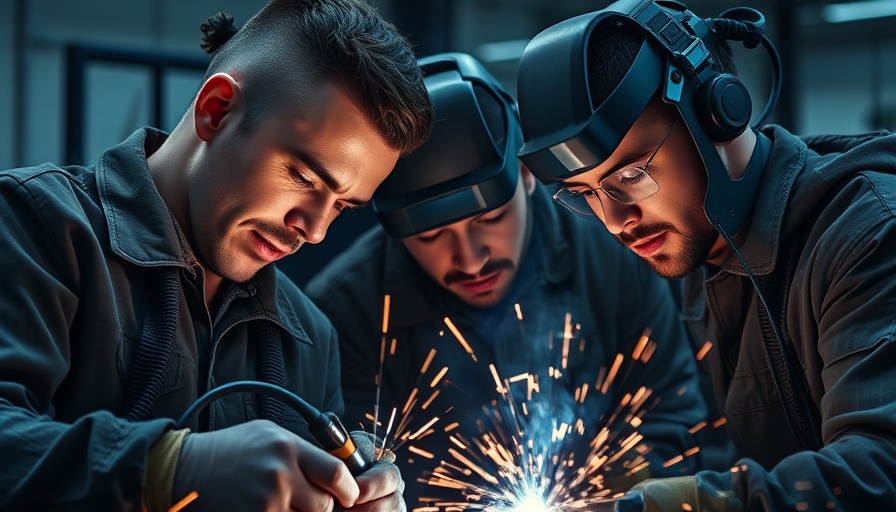
The Urgency of Workforce Development in Manufacturing
The manufacturing industry is at a crossroads, facing a significant challenge as a wave of experienced workers retires. This demographic shift is not just a matter of replacing old with new; it's about bridging the profound skills gap that threatens productivity and innovation in advanced industrial sectors. With rapid technological advancements and evolving job requirements, companies are finding that a lack of proficiency in new hires hampers their ability to compete in global markets.
Understanding the Skills Gap
Evidence suggests that advanced manufacturing roles like welding and machining require extensive training to master. As seasoned professionals exit the workforce, organizations are struggling to onboard new talent equipped with the necessary skills. A McKinsey report highlights a notable urgency in improving the time it takes for new employees to reach proficiency, a crucial factor when facing increasing production demands.
Technology's Role in Accelerating Learning
To combat these challenges, manufacturers must embrace modern training technologies. The integration of digital tools, such as AI-powered training programs and virtual simulations, can greatly reduce onboarding time. By utilizing these technologies, companies not only enhance the skillset of their workforce but also create an engaging learning environment that appeals to the tech-savvy newcomers.
Strategic Insights for Organizational Change
Manufacturers should look beyond mere reactive measures and focus on strategic plans that foster long-term organizational change. This includes investing in employee development programs that align with individual career paths while promoting interdisciplinary collaboration. By doing so, firms can break down silos that often reduce operational efficiency and limit innovative thinking.
The Importance of Performance Management
A critical component of addressing workforce challenges is enhancing performance management systems. Many manufacturers lack visibility into the performance across different teams due to traditional management structures. By adopting more integrated performance management practices, organizations can identify skill gaps and develop tailored training interventions, fostering a culture of continuous learning.
Real-World Applications and Case Studies
Several companies have paved the way by successfully implementing comprehensive workforce training programs. Their experiences reveal that investing in employee development translates to higher productivity levels and less turnover. For instance, a leading aerospace firm revamped its training protocols to compress the onboarding period, resulting in a significant leap in operational productivity.
Encouraging Workforce Engagement and Motivation
While technological solutions and strategic practices play a vital role, fostering an engaging working environment is essential. Employees need to perceive growth opportunities that align with their skills and aspirations. Recognizing achievements and offering competitive pay tied to skill progress promotes motivation and satisfaction, ultimately enhancing retention rates.
Taking Proactive Steps
Investing in the manufacturing workforce means future-proofing the industry. As manufacturers creatively address workforce shortcomings by leveraging technology and a strong performance management framework, they set the stage for enhanced productivity and innovation. Taking proactive steps now will ensure that companies not only survive but thrive in an ever-evolving economic landscape.
To explore more about how you can apply these insights into your workforce strategy, consider engaging with expert reports and data-driven analyses available in industry publications. These resources can provide further guidance on best practices for workforce development in manufacturing.
Write A Comment